We recently built a new access control solution for a life sciences company’s sterile lab environment, using a particularly elegant technical approach.
This client’s 10-room clean area included multiple interlocking doors with and without card access, and one three-door interlock. In this application we were asked to account for omni-directional and bi-directional traffic for areas of gowning, de-gowning, material handling, waste handling, and pressurized cross-contamination.
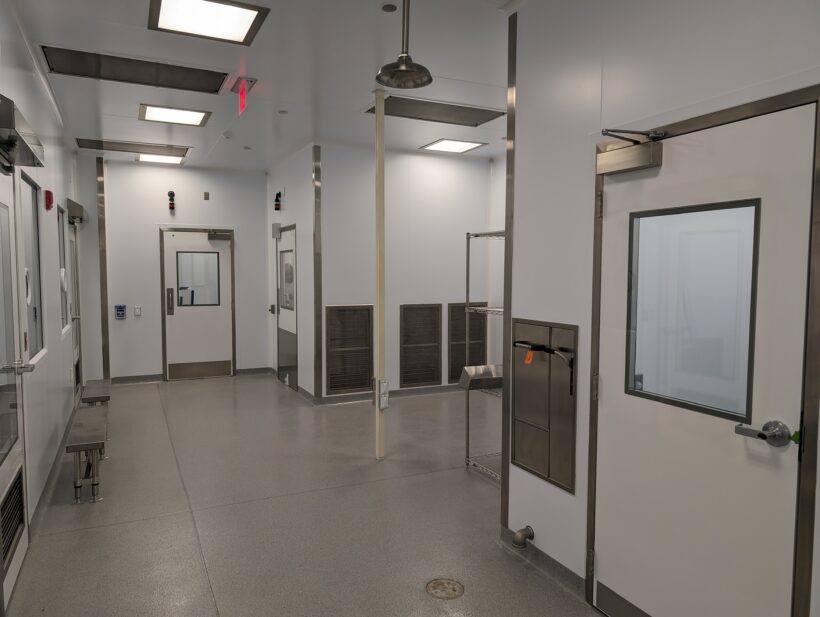
Customarily, a piece of hardware such as Von Duprin’s 9400 series interlock controller could be used to interlock multiple doors. These tried-and-true controllers offer several attractive features like expandability and a FAI (Fire Alarm Interface) input. (Both require additional hardware). In the case of multiple interlock spaces, each would need a dedicated controller and FAI input. Interlock controllers also need a sizable amount of space local to the doors and a dedicated high voltage power source.
One feasible alternative to that method would be to use an access control platform such as Genetec to collect a variety of inputs, and create a custom macro to determine the sequence of operations. The access control platform method is effective if your software interface allows enough flexibility to handle the programming. Yet the additional hardware costs and lack of open-ended programming on systems like Lenel and Software House make it hard to develop a standard process.
Secuni’s engineers instead developed a new solution utilizing PLCs (Programming Logic Controllers) designed by Automation Direct.
PLCs are typically utilized in HVAC and BAS systems. These small format modular units can be nested neatly inside of a power enclosure. The PLC utilizes the low voltage (24v) provided by any ACP to supervise inputs from several sources including door status, bond status, entry/exit requests, emergency over-rides, and any other environmental condition (pressure/temperature/vapor detection) which can be indicated by outputs from external devices.
Here’s a partial schematic from our as-built drawing, showing the PLCs.
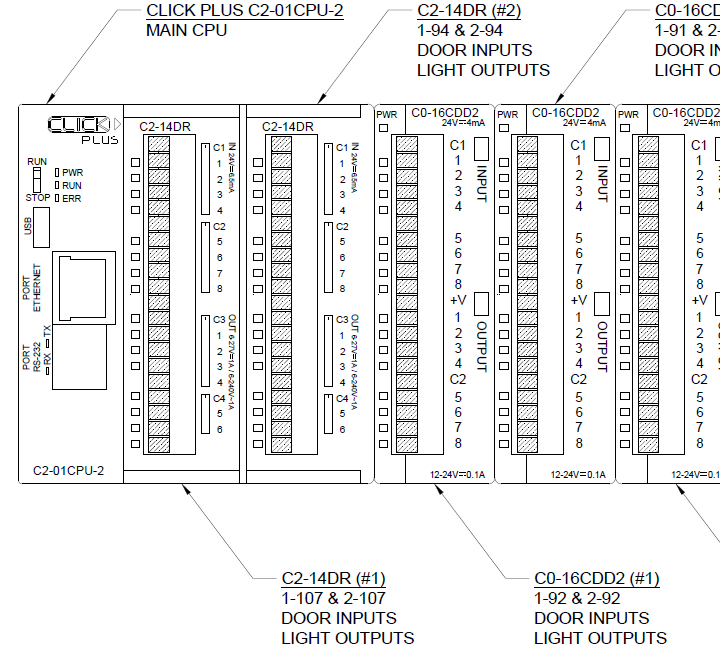
PLCs collect analog or digital input signals from multiple devices. These “events” can then be used to write custom programming sequences, which produce “actions” in the form of digital or analog outputs.
This approach allows for a consistent standardized approach to complex interlock solutions regardless of access control platform. PLCs also offer a significant cost reduction on the hardware side. Card access doors will still require a door controller, but non-card access doors will not require additional licensed hardware.
Cost savings are case by case depending on scope and system but will be quite meaningful considering the lack of licensing, need for electrician, and hardware costs.
We believe this method saved the client $50,000 over the customary interlocking door technical approaches.
PLCs can be monitored via network connection or function completely off-line in areas of concern. PLCs can also live on a BacNet protocol for automations integrations or be linked on a RS-485 Comm protocol.
One CPU can handle up to 8 downstream controllers, which means 8 interlocked areas with basic config.
PLCs programming can be stored onboard the CPU with back-ups loaded on the mounted SD slot or USB stick. Programming can be done directly via network/serial ports or remotely via IP interface.